
Profinet is an innovative and open standard among the most widespread in the world. Developed by Profibus International it is a communication system based on Industrial Ethernet. Becoming an international standard with IEC 61158 and defined in close cooperation with end users on the basis of IEEE 802, IEC 61158 and IEC 61784 standards, Profinet supports the integration of field devices for automation and time-critical applications. Profinet in turn includes two different protocols, Profinet CBA (Component Based Automation) based on access standards such as RPC/DCOM/OPC and modular applications, and Profinet IO designed for field and real-time applications.
Profinet IO, model, classes and devices
Combining the ease of use of Profibus DP with a standard Ethernet physical layer, Profinet IO offers the increased speed and ease of handling required by ever-increasing volumes of device data. Profinet IO features standardised functions for parameterization, diagnostics and alarms that are significantly more extensive than traditional bus systems.
With Profinet IO, the master-slave access methodology of Profibus-DP has been converted to the provider-consumer model for data exchange. The design of a Profinet IO system follows the same configuration as a Profibus system. But the following classes of devices are defined for Profinet IO:
IO Controller: This is generally the PLC on which the automation program is running. The IO Controller provides the output data to the configured IO Devices in its role as provider and is the consumer of the input data of the IO Devices.
IO Device: an IO Device is a distributed I/O field device that is connected to one or more IO Controllers via Profinet IO. It is comparable to the function of a slave in PROFIBUS. The IO Device is the supplier of input data and the consumer of output data.
IO Supervisor: can be a programming device or an HMI with commissioning or diagnostic purposes.
A system unit contains at least one IO Controller and one or more IO Devices. IO Supervisors are generally only temporarily integrated for commissioning or troubleshooting purposes.

Performance levels and conformity
Profinet communication has three performance levels covering the entire field of automation applications: 1) TCP, UDP and IP for non time-critical data, such as configuration operations; 2) Soft Real-Time (SRT) for time-critical process data, used in most industrial applications; 3) Isochronous Real-Time (IRT) for Motion Control and high performance applications.
Standard communication via the TCP-IP protocol gives average response times of around 100 ms. Communication via SRT Channel shows an improvement in transmission times of a factor of 10, with response times of around 10 ms. The key features of the Profinet standard include the simultaneous use of TCP-based and Real-Time communications; the standardised real time communication protocol for communications between components in distributed systems as well as for communications between controllers and decentralised peripherals; scalable real time communication. The scope of functions supported by Profinet IO is divided into Conformity classes (CC) which provide a set of minimum properties required by the protocol: CC-A (basic functions with Real-Time communication), CC_B (diagnostics and topology), CC-C (further implementation for IRT communication). The Conformity Classes also provide the basis for certification and wiring guidelines.

Real Time communication classes
Profinet IO also defines three classes of real-time communications, which for simplicity can be grouped into two main groups: Class 1 for Real Time (RT) communications in systems requiring cycles in the order of tens of milliseconds; Classes 2 and 3 for isochronous communication (i.e. with real-time data transfer at equidistant time intervals) and RealTime (IRT) in systems requiring cycles in the order of hundreds of microseconds and cycle time variations of less than 1 μs. The transmission speed can be 100 Mbit/s or 1 Gbit/s.
Profinet IO Class 1 (RT) is a variant in which the various devices are not synchronised and each operates with its own cycle time. At the beginning there is the transmission of cyclic RT data, followed by acyclic RT data, such as alarms. At the end a portion of the bandwidth is reserved for non real-time communication that can coexist on the same physical network (e.g. based on TCP/IP). In class 1 we try to achieve isochrony in software mode, relying on Ethernet priorities, with Profinet packets defined as priority 6 and managed by standard switches.
SENECA Profinet I/O
R-16DI-8DO-P proposed by SENECA is a mixed digital module with dual 10/100 Mbps Ethernet port and RT Class 1 support. The tool is designed for flexible wiring needs, reduced installation space, high I/O density applications with integrated Ethernet networking. R-16DI-8DO-P has 16 PNP/NPN digital inputs and 8 relay digital outputs with maximum capacity 30V/1A. The module is equipped with insulation between inputs, outputs and other low voltage circuits equal to 1,500 Vac. R-16DI-8DO supports Profinet IO communication and can be connected in Ethernet daisy chain mode with fault-bypass to ensure Ethernet connection even in case of failure of a module in the chain.
The configuration of the R-16DI-8DO-P module can be done via CODESYS softPLC software and Siemens TiA Portal/ Simatic / Step7 design environment. In any case it is necessary to first install the GSD (General Station Description) file, i.e. the XML or graphic file necessary for the configuration of each device on the Profinet IO network.
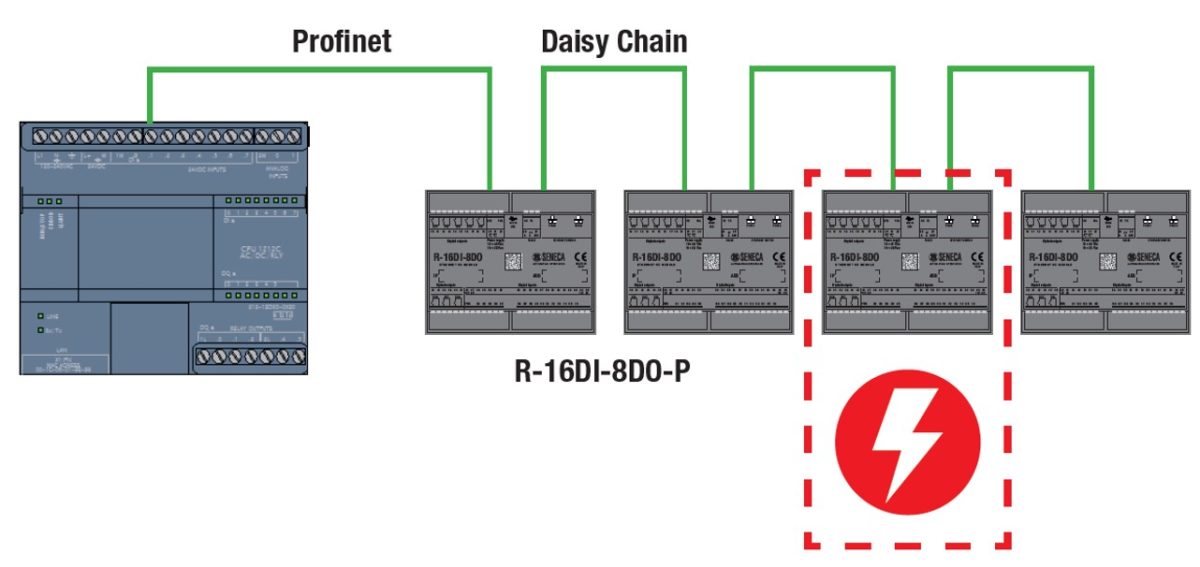