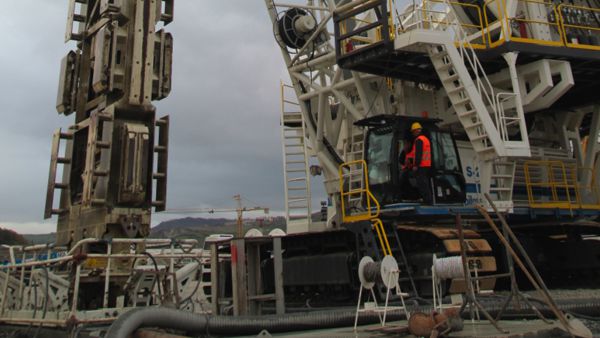
Founded in Cesena, Italy, in 1957 by Cavalier Davide Trevisani, the Trevi Group is a world leader in subsoil engineering for special foundations, tunnel excavation, soil consolidation, and the manufacture and marketing of specialized machinery and equipment for the sector. Among the reasons for Trevi Group’s success are internationalization and continuous integration and interchange between the two divisions: Trevi, which carries out special foundations and soil consolidations for major infrastructure projects (subways, dams, ports and docks, bridges, railway and highway lines, industrial and civil buildings), secures polluted sites, and builds and manages underground and automated parking lots; and Soilmec, which designs, manufactures, and markets machinery, equipment, and services for underground engineering. Parent company Trevi Finanziaria Industriale Spa has been listed on the Milan stock exchange since July 1999
Hydromill with depth record
Trevi Group has once again written an important page in subsurface engineering, thanks to the use of a newly developed Hydromill. Trevi has acquired the ability to create diaphragms up to 250 meters deep; a goal never before touched, and until now considered unthinkable. In fact, the depth’ of 250 meters exceeds by more than 100 meters the maximum limit never reached before, and thus represents a record, as much on the application level as on that of the knowledge needed to manage soil and deep water, as well as of the development of a machine capable of digging up to that height.
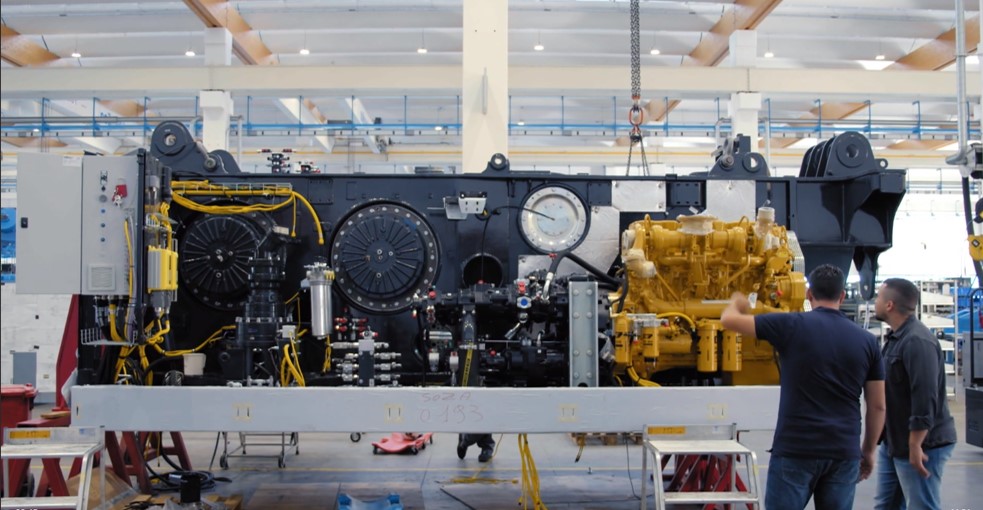
SENECA Technology
Hydromill cabling system and control panel are critical to reduce overall time and money expenditure: from planning and design to installation and commissioning and maintenance. SENECA’s data acquisition technology, represented by the fieldbus modules (Modbus, Ethernet, Profinet, CANopen) of the Z-PC Series, offers galvanic isolation and diagnostic functions integrated at the machine’s edge. This approach also offers the advantage of reduced footprint in the control cabinet due to the compactness of the required I/O modules.
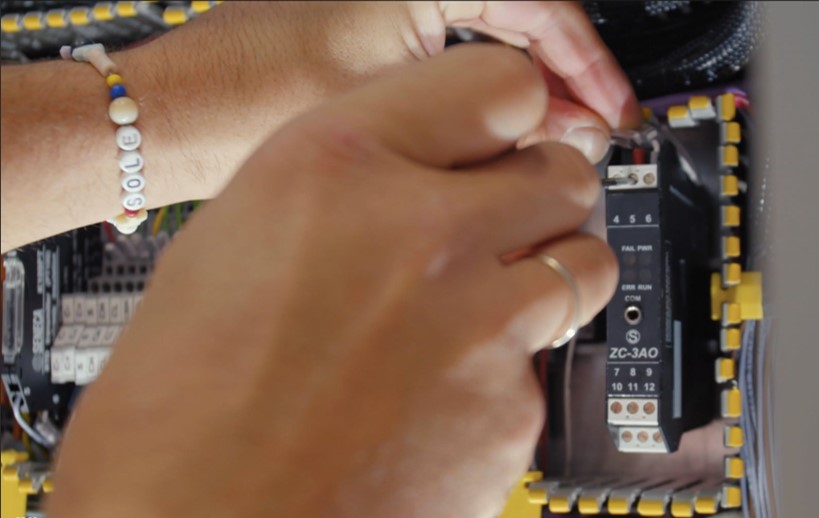
Watch here the episode of “Mezzi Speciali – Forgiati su Misura” on DMAX dedicated to the record-breaking hydrotiller